Embraer Develops Training Plan To Support Automatic Takeoff Capability
Embraer is developing a pilot training program for the industry’s first automatic takeoff system, which is to be introduced first on the E2 regional jet family. As the autotakeoff system mimics manual takeoff procedures, the manufacturer expects the training required to be simple.
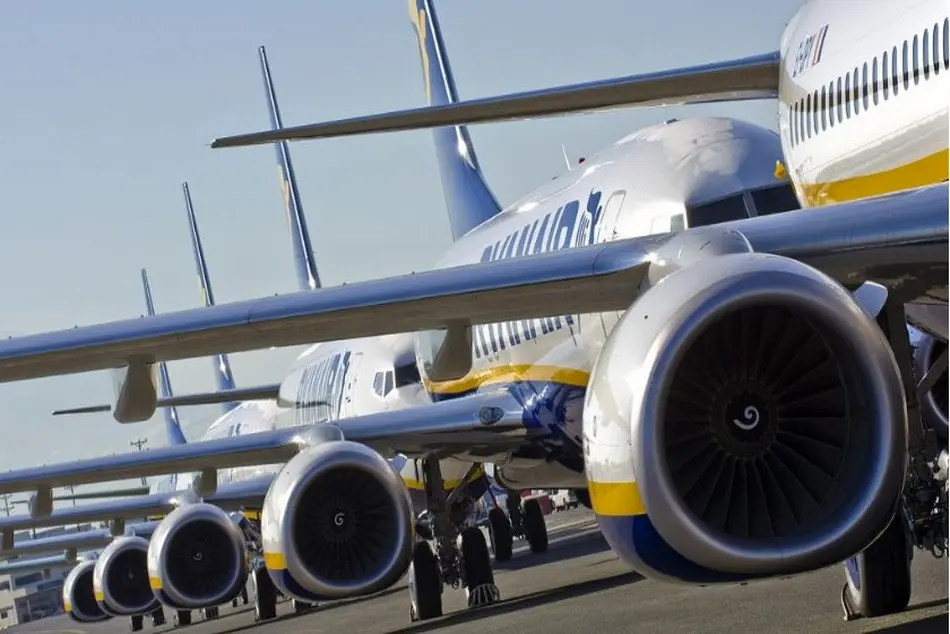
Embraer is developing a pilot training program for the industry’s first automatic takeoff system, which is to be introduced first on the E2 regional jet family. As the autotakeoff system mimics manual takeoff procedures, the manufacturer expects the training required to be simple.
“We think, because it is a novel system, we should have some training,” says Luis Carlos Affonso, Embraer senior vice president of engineering and technological development. “We have seen in the industry that sometimes you try to save on training, and this may then have adverse consequences.
“We believe that training just to explain how the system works, so that the pilot has full awareness of how it works, will prepare them to operate it,” he says. “We believe it is good practice to have this training. But it will be very simple, because the changes in terms of the operation are minimal.”
The Brazilian manufacturer introduced the Embraer Enhanced Takeoff System (E2TS) at the Farnborough International Airshow in July. The E2TS is a function of the E2 family’s fourth-generation full-authority fly-by-wire system, which provides a high level of integrity and availability with its triplex-redundant flight control computers and quadruplex air-data sensors, says Patrice London Guedes, E2TS technical leader. A retrofittable software upgrade, the E2TS is planned to be available in the fourth quarter of 2025.
The E2TS is designed to reduce takeoff distance by providing precise and consistent control of pitch angle, which increases the payload/range performance of longer aircraft taking off from short runways. The system also will increase safety, London says, reducing pilot workload in crosswinds and engine failures. From runway-limited London City Airport, the system will add 350 nm of range, Embraer calculates.
Takeoff distance is measured from brake release to an altitude of 35 ft., called the screen height. Long aircraft like the E195-E2 have a pitch limit to avoid tail strikes, and this sets the takeoff distance. With the E2TS, when the aircraft is a few feet in the air, the system automatically begins a continuous pitch increase to a higher angle, reaching screen height sooner.
When operating from a short runway, this reduction in takeoff distance can translate into more range for the same payload, more payload for the same route or a thrust reduction. The E2TS is being certified as a fail-passive system. “This means the system disengages with a single failure, and the pilot easily assumes control and safely continues the takeoff,” London says.
The E2TS is designed to mimic the manual takeoff procedure, with two key differences that require dedicated pilot training to be mandatory. After lining up on the runway, the pilot must first engage the system by calling up the E2TS page on the multifunction control display unit and pressing a button. An E2TS indication appears on the primary flight display.
The pilot also engages the autopilot and autothrottle on the ground. This is a change from the current procedures, which prohibit autopilot engagement before liftoff. This is not a certification rule but is a means of compliance, London says, and Embraer is discussing an alternate method of compliance with regulators to permit autopilot engagement on the ground.
The other key change comes during the takeoff roll. “The only thing you have to focus on is not to rotate the aircraft and allow the aircraft to rotate itself, because if you rotate it, the system will disengage,” says Affonso, who is type-rated in the E2 and has flown the E2TS.
At 200 ft. altitude, the E2TS hands over to the autopilot. “It is not that E2TS will give the aircraft back to the pilot; it is that the autopilot mode will move from E2TS to flightpath, which is the vertical mode of the autopilot. At 400 ft., the lateral mode engages . . . and you can take your hands off the yoke,” he says.
“The standard operating procedures are the same, the callouts, everything,” Affonso notes. “If E2TS fails, the callout is one the pilot is used to—‘autopilot, autopilot’—so they don’t need to learn anything new. Whenever a pilot hears ‘autopilot, autopilot,’ they know they have control.
“It’s amazing that the human-machine interface is the same. That’s why we believe the training will be very easy,” he continues. “Pilots need to know and be comfortable with how the system operates, but it will be second nature for them.”
Although designed to improve performance, the E2TS also will improve safety, London says. “In lateral directional control, the system is much more precise than the pilot, even in high crosswind conditions or with an engine failure,” he says. If an engine fails on takeoff, the E2TS will apply rudder to compensate. “It will not only rotate; it will take care of bank angle and also compensate for yaw,” he says.