Tech Feature: (No) Rocking the Boat
Seakeeper’s motion control technology can improve the performance of even the most impressive of workboats. Partnering with Seakeeper and Gladding-Hearn, the Charleston Pilots did just that, once again setting the bar for excellence.
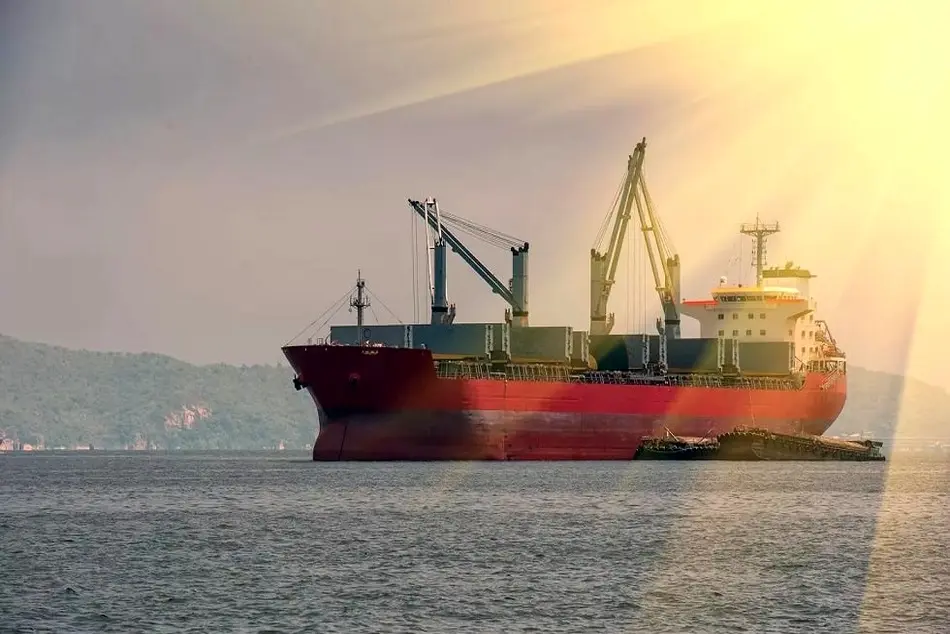
Seakeeper’s motion control technology can improve the performance of even the most impressive of workboats. Partnering with Seakeeper and Gladding-Hearn, the Charleston Pilots did just that, once again setting the bar for excellence.
On a beautiful Autumn afternoon in Charleston, SC, way back in 2014, MarineNews had the good fortune to attend the christening on the nation’s first dual purpose, rapid response vessel and pilot launch. As the first vessel to be designed for offshore salvage and firefighting requirements, Fort Ripley was also notably the first commercial application of Volvo Penta’s IPS drive propulsion.
At the time, the vessel also represented an interesting twist in the Charleston Branch Pilots’ business model. With a Tier III compliant propulsion arrangement that was designed to burn 30 percent less fuel than any of the other three vessels in the Charleston Pilot fleet, the vessel’s long range endurance has, over time, allowed it to respond to maritime events all along the mid-Atlantic coastline.
The new delivery was, in short, a welcome addition to the port of Charleston.“The Fort Ripley was designed to add the best combination of readiness and response capabilities to the Port of Charleston we could fit into a pilot launch,” says Captain W. Crayton Walters, President, Charleston Pilots. He added, “As our first post 9/11 new-build, and with the evolution of port contingency planning and emergency response objectives, we recognized that pilot vessels can, and in fact inherently do, serve in a readiness and response role concurrent with providing pilotage services. So, we built the FORT RIPLEY with additional features to enhance that readiness and best serve the port should an emergency occur.”
To that end, the Fort Ripley has been listed with the Coast Guard as an available vessel response plan asset since it was commissioned in 2014, and has responded to a number of emergencies including persons-in-the water, vessel and structure fires, and vessel sinkings. As February 2025 rolls on, this impressive platform is about to get even more capable.
Leveraging Trust, Experience, and Competence
As they looked to improve the already impressive capabilities of Fort Ripley, the Charleston Pilots naturally also looked to Gladding Hearn for help.
Captain Walters told MarineNews, “The Charleston Pilots first boat build with Gladding Hearn was in 1960. Ever since that first hull, we have had a long relationship with Gladding Hearn and Ray Hunt design. We have had many boats made to our specifications and needs, always asking for and receiving the best quality and workmanship around stable and safe pilot boats. GH has always delivered boats to us that are well designed, well made, backed by an outstanding company that stands by their work and product.”
According to Peter Duclos, President, Gladding-Hearn Shipbuilding, Gladding-Hearn and the Charleston Pilots have enjoyed an excellent relationship since their very first order. Paying the pilots the ultimate compliment, he adds, “They are a forward thinking organization and have pushed us on several occasions to develop new designs which have benefited the industry as a whole.”
Even as technology and materials changed over time, Charleston Pilots’ relationship with the Duclos family has been a constant since 1960. In this case, the Charleston Pilots are a return customer; something that shows real loyalty and trust. But Gladding Hearn is known for being the east coast’s busiest pilot boat builder, and for a long time. Duclos explains why, telling MarineNews, “We have delivered over 100 pilot boats since 1957. More than 30 pilot groups operate Gladding-Hearn boats; some of which have been resold several times.”
2014: A New Vessel Earns its Stripes
Even back in 2014, A guided tour and short excursion aboard the versatile vessel was ample proof of the workboat’s clever design, with scarcely a tremor in the vessel’s spacious and high tech wheelhouse even at speeds of 28+ KT. Looking back on that event, it is clear that Volvo Penta’s turnkey IPS propulsion package, then a novelty but now increasingly a staple of the North American workboat scene, would be a success.
The Fort Ripley, powered by triple Volvo Penta IPS drives, is a U.S. Coast Guard-certificated 64-ft. aluminum boat, owned by Southeast Ocean Response Services Inc. Built by Gladding-Hearn Shipbuilding, Duclos Corporation, and designed by C. Raymond Hunt Associates, the boat’s original primary mission was to allow ships to meet federal requirements for rapid offshore firefighting, salvage and emergency response, providing coverage between Morehead City, N.C., and St. Augustine, Fla. It was also equipped to serve as a fireboat in Charleston Harbor, a supply boat for ships at anchor and an additional launch for the Charleston Pilots and other marine operators in the region.
The three IPS drives, each powered by a commercially rated Volvo Penta D13-700 diesel engine, are independently steerable, with dual counter-rotating forward-facing propellers to maximize efficiency and increase maneuverability. The IPS can be controlled from the wheelhouse or either of the two aft docking stations using a three-axis joystick. The Dynamic Positioning System (DPS) provides fully automatic hands-off precise station-keeping under GPS control. The triple engine configuration allows the center engine to decouple from the drive and power a 3,500-GPM fire pump while the two outboard drives easily maneuver the vessel or maintain position automatically using DPS.
Even back then, the value of the boat was clear. “Fort Ripley is a truly revolutionary boat,” said Ron Huibers, President, Volvo Penta of the Americas. “The combination of the Hunt-designed hull and our IPS drives with DPS sets a new standard in terms of speed, maneuverability, fuel economy and seaworthiness to meet multiple mission requirements. This vessel represents the future of the next generation of multi-purpose response boats.”
Multi-missioned, economical to run, U.S.-built and designed, and environmentally compliant, Fort Ripley is arguably the quintessential definition of the modern workboat: nothing left to chance, and everything included. Improving on that achievement would be difficult, but as it turns out, not impossible. And, that’s where Seakeeper, a leader in marine motion control technology, comes in.
Bringing Stability to America’s Pilots
According to Seakeeper’s Director of Marketing, Kelsey Barrett, the Galveston Pilots' integration project was Seakeeper’s first U.S.-based pilot boat integration. She explains, “This ultimately serves as a great platform for demonstration and end-user feedback specific to this industry's use. The similarities between Seakeeper unit sizing, boat specifications, and harbor conditions when comparing Texas City and Fort Ripley, contributed to the confidence in performance.”
The technology is simple, actually. Seakeeper uses the physics of gyroscopes to eliminate up to 95% of boat roll. Inside a vacuum-enclosed sphere, a steel flywheel spins at speeds of up to 9,750 rpm. When the boat rolls, the Seakeeper tilts fore and aft (precesses), producing powerful gyroscopic power, known as angular momentum, to port and starboard to counteract the boat roll.
Regardless of where Seakeeper is installed, either on or off centerline, performance will remain the same. That’s because it’s attached to the structure of the vessel and will distribute the same forces throughout the hull. Barrett adds, “We do our best to install each Seakeeper midship-aft for optimal performance and longevity. A workboat is typically packed with equipment and accessories. In this case, if space does not allow for a single unit, there is the option to have two smaller units installed.”
Nevertheless, no matter which Seakeeper model a vessel requires, weight and space shouldn't be an issue. The dimensions and weights for each are available at seakeeper.com, but on average, the unit equates to 1.5-3% of the boat's overall weight.
Interested pilot organizations will ask what to expect and what kind of guarantees they will be afforded. For starters, Seakeeper can eliminate up to 95% of boat roll. Barrett explains further, “With the extra stability onboard, you can expect improved safety, scanning system precision, efficiency, and accuracy. Seakeeper allows you to depart in any sea condition with confidence,” and, she adds, “All products come with a standard 2-year/2,000-hour warranty with extended warranty options available.”
For the Charleston Pilots, the recent upgrades were a no-brainer. “The addition of the Seakeeper will certainly improve the FORT RIPLEY's capability supporting both pilotage and emergency response. Offering a more stable platform to transport pilots or responders will reduce fatigue and increase the safety of all operations onboard in support of every mission,” said Crayton Walters, adding quickly, “We are very excited that this mid-life retrofit will give us an even more versatile and effective offshore launch through the next phase of the FORT RIPLEY's service life, and the addition of the Seakeeper is certainly the most exciting upgrade in the package.”