Operators Connected by Technology Don’t Quit
Sometimes the truth hurts worse when everyone knows it. That’s precisely what "connected worker" technologies do. They disseminate at the organizational level your plant’s issues with quality, productivity and efficiency.
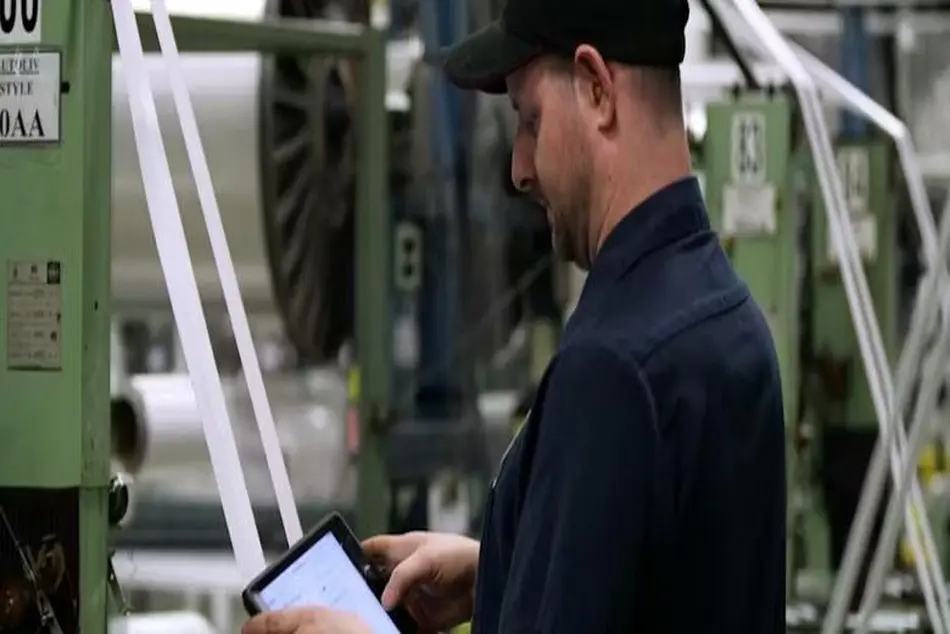
Sometimes the truth hurts worse when everyone knows it.
That’s precisely what "connected worker" technologies do. They disseminate at the organizational level your plant’s issues with quality, productivity and efficiency.
Employing the technology can therefore look very unattractive to some manufacturers, but what if that technology broadcasts success instead of failure and your operators can point at how their feedback, reported for all the company to see, led to those successes?
Connected worker technologies run the gamut from simple options like smartphones, tablets and boards mounted on walls or hanging from ceilings to advanced devices like augmented and mixed reality headsets. The pitch for all the technologies, low- and high-tech, remains the same: allowing operators on the floor to widely share and distribute information like machine health, cycle times and shift results.
This also means digitizing plant data rather than clinging to analog methods like pen-and-paper documents, mind-numbingly transferring data into Excel spreadsheets and databases, followed closely by the painstaking task of running queries and cobbling together reports that often contain outdated information and too late to serve any practical use.
Eric Whitley serves as the director of industrial transformation at software company L2L , formerly Leading2Lean, a company spun out from automobile safety device manufacturer Autoliv and born from its lean expertise . Whitley, who previously worked at Autoliv and McDonnell Douglas, also consults on maintenance and lean, teaches classes, hosts the Manufacturing Stream podcast and has “been in every type of factory you could possibly conjure up in your head.”
L2L recently released a report titled “What’s Holding Manufacturers Back in 2024?” that discusses the impact of the manufacturing labor shortage, the state of workplace communication and manufacturers’ progress digitizing factory floors. IndustryWeek sat down with Whitley to discuss the report’s conclusions. This conversation has been edited for length and clarity.
IndustryWeek: 46% of respondents said there have been significant resignations at their organization in the past year. Can we define “significant?”
Eric Whitley: I don’t know that we actually have a data point around what that means by "significant" resignation. But what we see is there are a lot of folks who come into manufacturing and then move on.
Over the years that I’ve done consulting and teaching and have been in all these different industries, I see where people get caught up into the thought process of “We make donuts, so we’re different than the guy who makes pastries,” or “We’re totally different than the automotive industry, or the people who make packaging.” The fact of the matter is, if you look at a manufacturing plant, there are people, there are machines. Those machines have basic principles to them. So what we’re seeing is that people can actually move from manufacturing plant to manufacturing plant, regardless of what sector they’re in, and pick right up.
IndustryWeek: 75% of respondents said they noticed a lack of skilled workers in the market in the past year. How do we define “skilled?”
Eric Whitley: What happens when you have a fault reset? What happens when you have a jam? How do you monitor it? How do you turn it on? I think those are the skills we’re talking about. Just being able to go in and run a production line. Basic skills. And that’s why, going back to our last question, that’s why it’s so easy for somebody to leave one production line making donuts and go down the street and go to the next production line that’s making airbags, because they have this general mechanical ability. Ten years ago, we were talking to people that had 30 years in a manufacturing plant, and now the worker in the manufacturing plant, they may only have been in there three years. That is just a general lack of experience working in manufacturing.