Fast 5: Dowty Pursues Next-Gen Aircraft Propeller Blades
Jonathan Chestney, engineering leader at GE Aerospace subsidiary Dowty, speaks with Aviation Week Network about advances in aircraft propeller blade design and their impacts on maintenance processes.
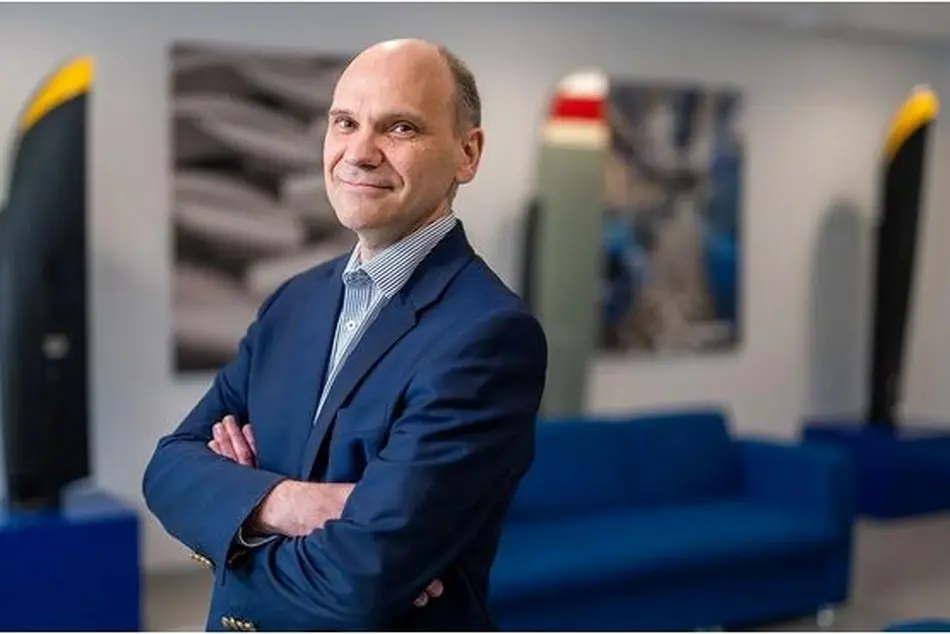
Jonathan Chestney, engineering leader at GE Aerospace subsidiary Dowty, speaks with Aviation Week Network about advances in aircraft propeller blade design and their impacts on maintenance processes.
How are you defining the next generation of composite propeller blades?
The drive for sustainability has brought about renewed interest in propellers. We are facing arguably the greatest opportunity for propellers since the first conversion of a jet engine into a turboprop configuration in the 1940s. The potential exists to expand beyond current established boundaries to respond to the industry need for reduction of carbon.
Dowty has been focusing its efforts on areas of efficiency, speed and noise to ensure that we are fulfilling our purpose to promote the future of sustainable propeller flight. Enhancement in analysis techniques such as computational fluid dynamics, supported by testing, has demonstrated that meaningful improvements in both efficiency and noise can be achieved.
Blade shapes are becoming ever more complex to deliver these improvements, requiring continued innovation in the structure to ensure that safety, durability and reliability are maintained. Again, analysis tool advancements have been required to ensure structural performance keeps track with aero-acoustic performance. The flexibility afforded by use of polymer matrix composites is perfectly suited to the needs of these advanced blade structures. Dowty has been working with composite blades for over 50 years, with its first all-composite blade entering service on the Saab 340 aircraft in 1984.
Is the automation of blade manufacturing a significant challenge?
Many techniques have been developed, primarily around aerostructures where deposition rates are the main driver, but blades require complex curvature with small radii to be achieved and this limits the use of many automation paths. The use of braiding has been popular, and continued development of these techniques has proven most beneficial for blades. This continues to be the case for the latest blade shapes.
Manufacturing techniques must also be capable of industrialization to deliver at the rates necessary for meaningful environmental change within the committed industry timescales. Automation is just one element of the solution; the full benefits of digital technology are also critical to maximize efficiencies and create the foundations of the digital twin necessary to achieve through-life cost-effectiveness.
How are newer, more efficient fuel sources like sustainable aviation fuel (SAF) and electric propulsion impacting propeller manufacturing?
There is no clear path forward beyond incremental improvements with today’s propulsion technologies, and we are nearing the limits of what can be achieved with thermal efficiency gains in gas turbines. The industry is looking forward with alternative fuels, including SAF and hydrogen, and increasing levels of electrification.
We are aligning our technology roadmaps with requirements from the wide range of disruptive powertrain technologies, including fully electric, hybrid-electric, hydrogen fuel cell (liquid and gaseous), SAF, hydrogen for combustion and open rotor configurations.
These emerging technologies offer varying degrees of promise but there are questions still to be answered about feasibility and cost-effectiveness. We need to be ready to accommodate all options, especially since one of the few points of agreement in the industry is that no one solution will fully address the sustainability need.
What are the key characteristics emerging for the future manufacturing of propellers?
Firstly, weight: the use of composites in blades delivers valuable weight benefit, but this must be accompanied by similar focus on the remainder of the propeller system. The use of composite in fairings, low-weight high-strength metal alloys and application of additive techniques are all being explored.
We also consider industrialization: it is vital that manufacturing technology is scalable and ready to deliver at rate.
Finally, environmental sustainability is one of the propeller imperatives that must be met. Life-cycle analysis has shown that, while aerodynamic performance is easily the most important factor for propellers, reduction of carbon through the manufacturing process will always require focus, too. Consideration of raw materials, energy usage in manufacture, and design for recyclability are all factors vital for future manufacturing technology.
Are technologies evolving quickly enough to cater to new composite repairs?
Product robustness and maintainability have always been priorities for Dowty, and propellers are designed with repairability in mind. One aspect that we consider through the product development process is the ability to maintain equipment with existing, available technology, including inspection and repair techniques, wherever possible.
Exciting technologies are emerging that will simplify and improve inspection. Some may be integrated into structures during manufacture, and others utilized in repair shops. Both should reduce maintenance costs and potentially improve the safety of repair activities. We also seek to improve our repair techniques in parallel with manufacturing techniques so that maintenance and acquisition costs are minimized.