CFM Leap 1 Durability Upgrade Awarded FAA-EASA Certification
A newly developed high-pressure turbine (HPT) upgrade kit to increase CFM Leap 1A time-on-wing has been cleared for use after receiving FAA and European Union Aviation Safety Agency (EASA) certification.
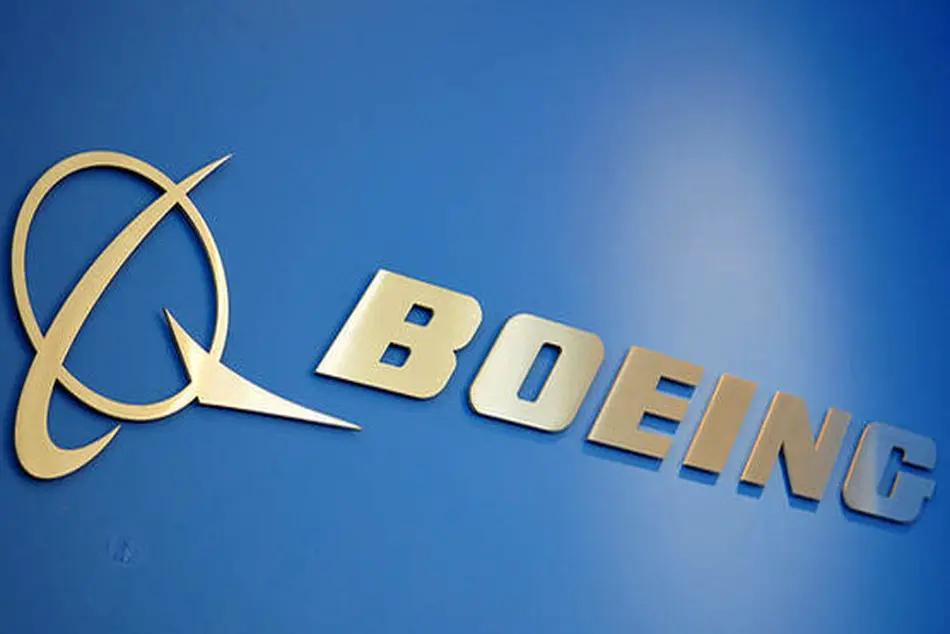
A newly developed high-pressure turbine (HPT) upgrade kit to increase CFM Leap 1A time-on-wing has been cleared for use after receiving FAA and European Union Aviation Safety Agency (EASA) certification.
The kit, which includes new HPT stage 1 blades, nozzles and forward inner nozzle supports, is the latest part of a broader series of upgrades designed by the GE Aerospace-Safran joint venture to improve durability—particularly for Airbus A320neo operators in the hot and harsh environments of the Middle East and Asia. The package is aimed at bringing the Leap 1 up to CFM56-like time-on-wing levels.
Certification comes after a long-running series of dust ingestion tests on the Leap 1A which were conducted on a specially developed rig in GE’s Evendale, Ohio, facility using bespoke material to replicate the pollutants and dust found in some areas of the world. After much trial and error, the company says it is now able to reproduce the premature wear, tear and failure modes found on the baseline Leap 1 first stage HPT blades.
Kit production is now getting underway, says Mohamed Ali, VP and general manager of engineering for GE Aerospace. “We’ll start first with the MRO shops—giving the medicine to those engines or customers who most need it in those harsh environments,” Ali said. “Then there’s a cut-into production engines plan that will go into full swing 100% over the next several months.”
Also known as CMAS (calcium-magnesium-alumino-silicate) tests, the dust ingestion trials evaluated the interaction of molten particles with the thermal barrier coatings (TBC) that protect the turbine blades. TBCs are key to enabling the engine to operate at temperatures up to 1,200 deg C, and CMAS issues can degrade coating performance, leading to blade erosion and—in worst cases—component failure.
The dust used in the CMAS has a consistency like talcum powder and was specially created for the tests by geologists and chemists. It represents particulate sizes and consistency typically found all the way from ground level up to mid-altitudes throughout areas like the Middle East and the Indian sub-continent.
Improvements included in the kit are mostly focused on the pattern and passageways of the blade’s internal cooling system as well as revised thermal barrier coatings. Following validation tests on the Leap 1A, CFM is conducting tests on the same upgrade in the Leap 1B, which powers Boeing’s 737 MAX.
“We are applying that same improved methodology on the Leap 1B and will be introduced at the time that will meet the customer needs. We feel very confident about it,” Ali says. “With the -1B, we have actually turned on and have been running the failure modes, and we’re in the process of turning it off right now with the new design equivalent to the -1A.”
Other fixes developed and now introduced to improve Leap 1 durability include an anti-coking reverse bleed system (RBS), which activates when the engine is shut down to keep the fuel nozzles cool. The induction of cooling air by a blower counters the coking problem, which can occur when residual heat in the engine core hardware “soaks back” after shutdown. The heat causes hard deposits of solid carbon to build up, which eventually shortens time-on-wing between overhauls and in some extreme cases has even caused in-flight shutdowns.
Additional upgrades also recently introduced include a redesigned starter air valve housing and associated solenoid for the A320neo engine, as well as a redesigned wear couple housing around the No. 3 bearing in both the Leap 1A and B to counter a non-synchronous vibration which, in some worst cases, has caused high pressure compressor stalls.