Building The World’s First LNG-Powered ConRo
El Coquí, the Commitment-class ship named after a tiny Puerto Rican frog, was delivered to Crowley Maritime Corporation (Crowley) from VT Halter Marine’s Mississippi yard on 20 July 2018. Hailed “the cargo ship of the future”, the vessel has been flying the flag as one of the world’s most technologically advanced and eco-friendly Combination Container Roll-on/Roll off (ConRo) ships.
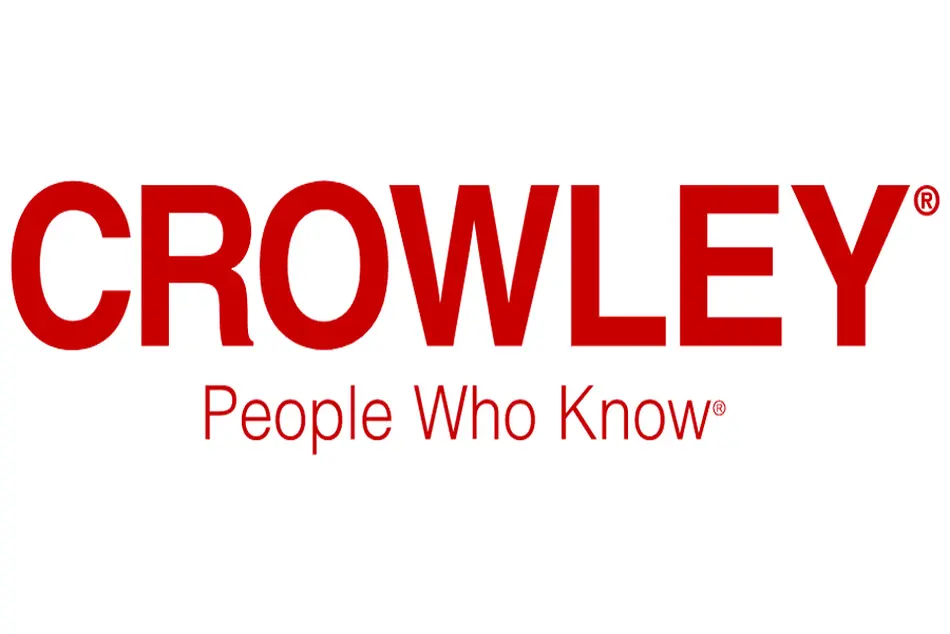
El Coquí, the Commitment-class ship named after a tiny Puerto Rican frog, was delivered to Crowley Maritime Corporation (Crowley) from VT Halter Marine’s Mississippi yard on 20 July 2018. Hailed “the cargo ship of the future”, the vessel has been flying the flag as one of the world’s most technologically advanced and eco-friendly Combination Container Roll-on/Roll off (ConRo) ships.
The El Coquí is, in fact, the first of two liquefied natural gas (LNG)-powered ConRo ships commissioned for Crowley’s shipping and logistics services between Jacksonville, Fla. and San Juan, Puerto Rico. Like her sister ship Taíno, El Coquí was constructed under the US Jones Act federal statute and is able to transport up to 2,400 twenty-foot-equivalent container units (TEUs) and a mix of nearly 400 cars and larger vehicles in its enclosed, ventilated and weather-tight Roll-on/Roll-off decks.
Buck Younger, Vice President of Engineering at VT Halter Marine, has been working on the ConRo programme since joining the company in 2013. “As functional design manager and programme engineer on the programme, I worked closely with the naval architects, mechanical engineers, electrical engineers and designers responsible for the vessel. Given the technological breakthroughs we hoped to achieve with the El Coquí, the programme was definitely an exciting challenge right from the onset,” Buck recalled.
An important consideration in the development of El Coquí was the requirement to use LNG fuel – a move aligned to impending International Maritime Organisation (IMO) regulations on lowering shipboard emissions. Buck explained, “The slow speed main engine, which runs on a high press diesel cycle, was specially selected for its ability to offer the lowest levels of methane slip, which accounts for cleaner methane emissions. Care was also taken in the design of the fuel gas system to trap and reuse any methane discharge associated with system purging. The customer brief was to achieve zero methane discharge!”
Another key consideration was the requirement to locate the LNG storage tanks and LNG pump room below the main deck. In the absence of an international safety code governing LNG-powered ship designs at the time, the team adopted the IMO Interim Guidelines MSC 285(86) and United States Coast Guard (USCG) Policy Letter 01-12 instead. This required close collaboration with DNV GL and USCG. “I can tell you that El Coquí was the first LNG ConRo to be approved by the USCG!” Buck revealed with a chuckle.
Efforts were also invested to insulate the vessel’s steel plates against potential LNG spillage on board. Besides locating the LNG storage and pump room in a stainless steel room below deck, the team insisted on the use of IMO Type C double-wall vacuum-insulated LNG storage tanks, which were built for high resistance to cracks and fractures. These tanks offered a 58-day hold-time compared to the Class requirement of 21 days, thereby prolonging the efficient storage of LNG while eliminating the risk of unlikely leaks in the inner tank.
Other green ship innovations incorporated on board the El Coquí included two ballast water treatment units that comply with regulations on the discharge of ballast water; an oily water separator that prevents the discharge of oil and gasoline overboard; and the use of double-wall vacuum-insulated stainless-steel gas pipes for the safe conveyance of LNG.
All in all, the successful delivery of El Coquí marked an important milestone in shipbuilding and engineering for VT Halter Marine – one that was driven by environmental stewardship. “For all of us working on the El Coquí, this has been the result of clear focus, strong discipline and good teamwork in meeting customer requirements. On many occasions, the team had risen to the challenges of working across cultures with designers in Germany, Denmark, Poland and Norway, establishing new weld procedures and participating in workforce re-training to integrate various vessel components so that the functionality, producibility and maintainability of the ship can be optimised throughout the design phase.
“We held regular face-to-face meetings, conducted weekly teleconferences and utilised 3D product modelling to review design adjustments with all parties online in real time. To ensure service responsiveness, we even stationed one of our engineers in Poland, where the facilities of a key subcontractor is based!” he elaborated.
Last but not least, the development process and experience have been deeply satisfying for Buck on a personal level. “For me, the greatest reward was seeing the ship come to life and operating in the customer’s fleet. That’s what all the hard work and sacrifices were ultimately for,” he said with a broad smile.
Source: ST Engineering