Catching up on rolling stock fire protection in Vienna
Amodest but engaged group of rail professionals with expertise in protection and control of fires gathered in Vienna, Austria, last week for the annual Fire Protection of Rolling Stock (FPRS) conference.
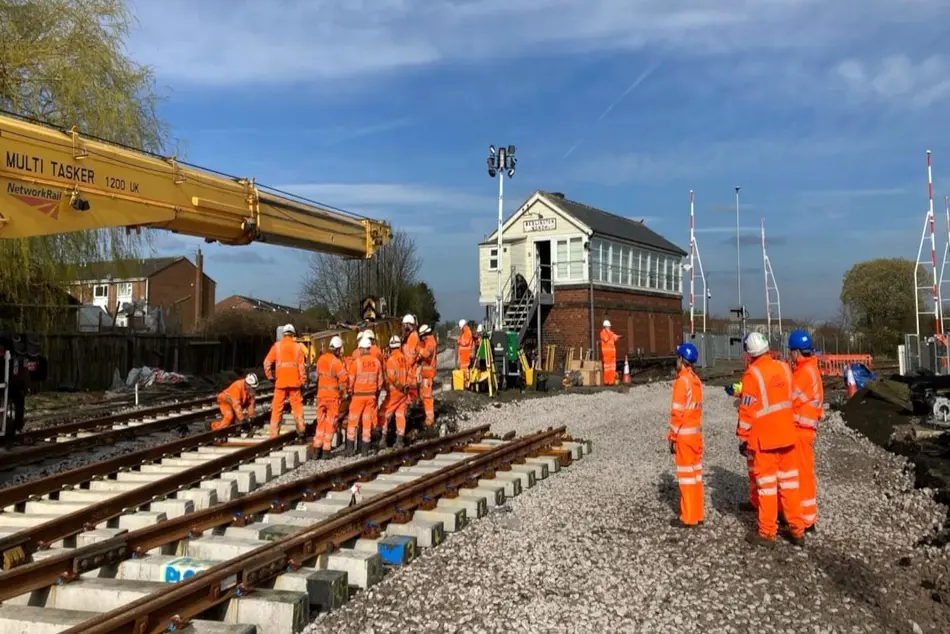
Amodest but engaged group of rail professionals with expertise in protection and control of fires gathered in Vienna, Austria, last week for the annual Fire Protection of Rolling Stock (FPRS) conference.
The complexity and importance of a wide range of regulations, spanning various jurisdictions, was a key element of discussions. While recent years can be accurately described as a time of great change, discussions on new propulsion methods and the growth of driverless systems show the pace of change is not slowing any time soon.
Attendees and speakers arrived from across the industry and around the world, with OEMs, rolling stock developers, fire safety tech vendors, train operating companies, and national and international regulators opining on the best ways forward.
British Standards, EU TSIs, Chinese safety checks
Discussions on standards and regulations are always at the forefront of FPRS, and this year was no different. The event is often used as an opportunity to hear from colleagues in different jurisdictions and understand what they are doing and why.
Although the European Union Agency for Railways (ERA) does not widely regulate the way European operators institute fire protection, its fixed installations and rolling stock unit head Olivier Piron opened this year’s event with an overview of how it does create Technical Specifications for Interoperability (TSI) and its work to harmonise and simplify European railway regulations.
Piron explained the process of discussions with working groups from industry, through to agreement with the European Commission in Brussels. While the process might seem complicated, its purpose is remarkably clear. European member states still have the right to implement national regulations, but the ERA works to ensure that cross-border travel remains viable by ensuring that these national laws do not contravene EU law. A key strategy has been analysis of the 14,000 national laws across the EU in 2016, and a reduction via harmonisation that means in 2025 there are only around 800 such laws.
He also highlighted EN-45545/2 as an overarching European regulation that the ERA works alongside with its TSI’s to ensure full compliance without onerous complexities for operators and manufacturers.
FPRS then heard from the author of a new UK design manual, which intends to centralise both regulations and best practices for fire protection when building new rail stations.
Network Rail’s John Boyce wrote the new Fire Safety Design Manual for Rail Stations NR/GN/CIV/300/03, published in June 2024. Surprisingly, this is the first time such regulations and British Standards have been published in a single document.
From the regulations managing the established networks around Europe, the conference moved on to the challenges of developing new technologies – and the challenges associated with developing the regulations to manage them.
Dafa Jiang of Chinese rolling stock manufacturer CRRC explained the development, testing, and certification of larger and more widespread use of lithium-ion batteries and the exciting moves being made in hydrogen railway propulsion technologies.
“In China for lithium batteries we have already established a standard system, so we have external assessors to evaluate the safety based on the norms. But for hydrogen fuel cells, we have external access trying to work with us to have a safety evaluation, but we still don’t have approved standards and norms to tell us what kind of design we should have,” he explained.
Maintaining and improving
Along with commercial addresses on new technology and tools at railways’ disposal, the conference heard from an expert on rolling stock maintenance, Keith Mack from London North East Rail, operating on the UK’s East Coast Mainline.
Although the general work of maintenance professionals on the railways is underestimated and sometimes under-resourced, Mack said improvements to the understanding of maintaining rolling stock and fire protection technology are leading to better results. (“You have to have suitable line workshop facilities. The days of doing this job down to feel, they’re gone. When I started work with maintaining coaches out in the yard, there’s no pit, there’s no roof, no nothing, we’re out in the cold, out in the snow. It’s not really a place to repair trains, the modern train wouldn’t survive.”)
Battery technology and the tools that have been developed alongside battery traction technology might seem straightforward, Mack said, but proper operation requires proper maintenance too.
Mack commented: “We heard about all the traction packs and all the monitoring that goes into them. That’s all very well, but what we need to remember is, if the maintenance we carry out is not going to prevent a thermal runaway, a thermal runaway is going to happen irrespective, all we can do is minimise the risks of that by looking after them properly. So look at [a] traction battery case. It’s not just the battery case, it’s all the peripheral components that make it all up, and we need to be assured fire protection systems remain [in] operation no matter what.
“It’s no different from cleaning around a diesel engine. You still have to do the same things. Cooling, fluid pipes, hoses, connections are all important. Fire extinguishing agent pipe work, hoses, connections; safety labels have to be clear, impacting damage guarantee to be present and fully functional. If you do all that, at least you can minimise the possibility of having a thermal runaway.”
But that’s not to say that modern advances on the railways are without maintenance applications.
A key benefit in recent years can be seen in real-time reporting of data analysis, and new physical tools to predict “roller bearing defects before failure”, Mack points out.
“We can also detect new lubricant degradation. This is done via line side or onboard thermal imaging. It shows the heat from roller bearings.”
This may or may not lead to fewer maintenance interventions, but Mack’s point is that it will lead to more efficient maintenance – and therefore operations – for modern railways.
But away from the tech, there is a big issue brewing in the UK railway sector – as pointed out by both Mack and Transport for the North (TfN) specification manager Daisy Chapman-Chamberlain pointed out.
“We face a huge number of our skilled workers retiring out of the sector, and we have to ensure that we can retain their knowledge and their skills before they leave. Otherwise we risk falling into the pitfall of short corporate and short government memory. One third of the UK’s rail industry workforce is aged 50 or over, and… we’ve got a very small increase in the number of younger workers, but it’s not sufficient to replace 47,000 employees,” Chapman-Chamberlain explained.
Where this intersects with fire safety for rolling stock and the wider railway is clear.
“It’s not just about transferring that knowledge, because anyone can learn the standards, but it’s also about learning the understanding and interpretation of the standards, the reason that they exist, and actually not losing that memory of when an incident doesn’t happen for several decades, and you do have a younger workforce, questions are asked about, ‘do we really need the standard? Maybe you can change it. Maybe you can lighten it,’ and then suddenly you’re on a very slippery slope to reducing safety,” Chapman-Chamberlain explained.
“We need trained, assessed staff. We need them to have system knowledge, and we need to process checks to make sure they do what they should do. These people also need to have non-technical skills in terms of their awareness of what they’re doing, why they’re doing it,” Mack added.
They need to be capable of doing it in times where maybe they’re tired or weak, and they need to be able to record that. They need to be able to feedback. Is the task rubbish? Can you do the task? There’s no point in just carrying on with this stuff, but you can’t actually do it… But that’s what’s written so it’s OK. It’s not OK!”
The challenge is to have well-trained staff who are confident with escalating problems and understanding what can be amended, and what is safety-critical in the job.
Along with regulatory evolutions and how best to use data and technology like AI in fire protection, the challenge of an aging workforce was a central challenge discussed in Vienna. Although much of the conversation flowed in the direction of progress, and problems the industry was on the way to solving, it seems longer term problems were more of a worry to delegates.
Railway Technology was a partner to the event organiser, ARENA, which is a sister company under the GlobalData umbrella.